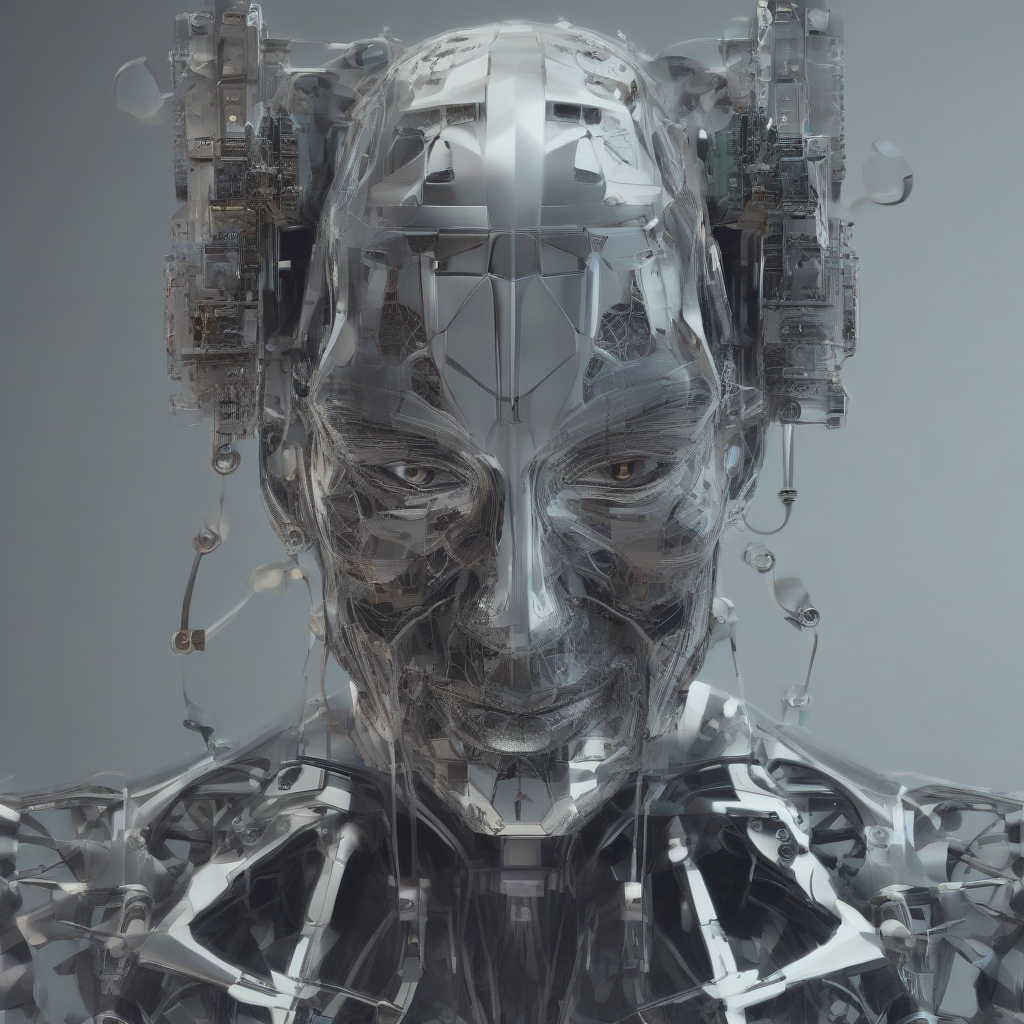
The Comprehensive Guide to Heat Exchanger Replacement: A Deep Dive into Types, Procedures, and Considerations
Heat exchangers are critical components in numerous industrial and domestic applications, responsible for efficient heat transfer between two fluids. Over time, these components degrade due to corrosion, fouling, and general wear and tear, necessitating replacement. This comprehensive guide explores the intricacies of heat exchanger replacement, covering various types, procedures, and crucial considerations to ensure a successful and safe operation.
Understanding Heat Exchanger Types
Before delving into the replacement process, understanding the different types of heat exchangers is crucial. The choice of heat exchanger significantly impacts the replacement procedure.
- Shell and Tube Heat Exchangers: These are among the most common types, consisting of a shell containing a bundle of tubes. Fluid flows through the tubes, while another fluid flows around them, facilitating heat transfer. Replacement often involves removing the entire shell and tube bundle.
- Plate and Frame Heat Exchangers: Composed of stacked plates with channels for fluid flow, these are easily disassembled and cleaned. Replacement usually involves replacing individual plates or the entire plate pack, depending on the extent of damage.
- Air-Cooled Heat Exchangers: These exchangers use air as the cooling medium, typically employing finned tubes to maximize surface area for heat transfer. Replacement involves replacing the entire unit or individual sections, depending on design.
- Brazed Plate Heat Exchangers: These are compact and efficient, but repairs are generally not feasible. Replacement is usually required if damage occurs.
- Spiral Heat Exchangers: Characterized by spirally wound channels, these are robust and efficient. Replacement is often a more complex undertaking due to their design.
Factors Influencing Heat Exchanger Replacement
Several factors influence the decision to replace a heat exchanger and the process itself.
- Deterioration and Efficiency: Reduced efficiency due to fouling, corrosion, or scaling necessitates replacement. Regular inspections and performance monitoring are essential.
- Cost-Benefit Analysis: Weighing the cost of repair versus replacement is crucial. Extensive damage may render repair uneconomical.
- Safety Concerns: Leaks, cracks, or other structural damage can pose safety risks, demanding immediate replacement.
- Process Requirements: The specific demands of the process using the heat exchanger influence the choice of replacement component and the replacement procedure itself.
- Availability of Spare Parts: Access to replacement parts and the lead time for procurement impact the replacement timeline.
Step-by-Step Heat Exchanger Replacement Procedure (General Outline)
The specific procedure varies depending on the heat exchanger type and its application. However, a general outline includes the following steps:
- System Isolation and Shutdown: Safely isolate the heat exchanger from the system and shut down the process. This is crucial for safety and preventing damage.
- Fluid Drainage and Flushing: Drain all fluids from the heat exchanger and flush it thoroughly to remove any remaining contaminants. Appropriate disposal procedures for the fluids must be followed.
- Disassembly: Carefully disassemble the heat exchanger according to its specific design. This may involve removing bolts, clamps, or other fasteners. Detailed diagrams and manuals are essential.
- Inspection and Assessment: Thoroughly inspect the old heat exchanger to identify the cause of failure. This helps in selecting the appropriate replacement and preventing future issues.
- Installation of New Heat Exchanger: Install the new heat exchanger, ensuring proper alignment and connections. Follow the manufacturer’s instructions carefully.
- System Reassembly: Reassemble the system, carefully checking all connections for leaks or damage.
- Leak Testing: Conduct a thorough leak test to ensure the integrity of all connections and the new heat exchanger.
- System Startup and Commissioning: Start up the system gradually, monitoring its performance to ensure proper operation.
- Documentation: Maintain detailed records of the replacement process, including dates, parts used, and any observations.
Safety Precautions During Heat Exchanger Replacement
Heat exchanger replacement involves working with potentially hazardous materials and systems. Strict adherence to safety protocols is paramount.
- Lockout/Tagout Procedures: Implement lockout/tagout procedures to prevent accidental energization of the system.
- Personal Protective Equipment (PPE): Wear appropriate PPE, including safety glasses, gloves, and protective clothing.
- Proper Handling of Fluids: Handle fluids appropriately, following safety data sheets (SDS) and disposing of them correctly.
- Confined Space Entry: If working within a confined space, follow appropriate procedures and obtain necessary permits.
- Lifting and Handling: Use appropriate lifting equipment and techniques to avoid injuries.
Specialized Considerations for Different Heat Exchanger Types
The replacement process varies considerably depending on the type of heat exchanger.
Shell and Tube Heat Exchangers
- Tube bundle removal and reinstallation requires specialized tools and expertise.
- Cleaning the shell side is crucial to prevent fouling of the new bundle.
- Careful alignment of the tube bundle is essential for efficient heat transfer.
Plate and Frame Heat Exchangers
- Individual plates can often be replaced, reducing the cost compared to a full unit replacement.
- Gasket replacement is essential to prevent leaks.
- Proper plate alignment and gasket seating are crucial for effective operation.
Air-Cooled Heat Exchangers
- Fan motor and drive system inspection should be included.
- Fin damage assessment is critical to ensure efficient heat transfer.
- Careful handling of fins is necessary to avoid damage during installation.
Troubleshooting Common Issues During Replacement
- Leaks: Thoroughly inspect all connections for leaks and address them immediately.
- Misalignment: Ensure proper alignment of the heat exchanger to prevent inefficient operation.
- Improper Gasket Installation: Follow manufacturer instructions for proper gasket installation.
- Tube Fouling: Prevent future fouling by implementing proper cleaning and maintenance procedures.
Conclusion (Omitted as per instructions)