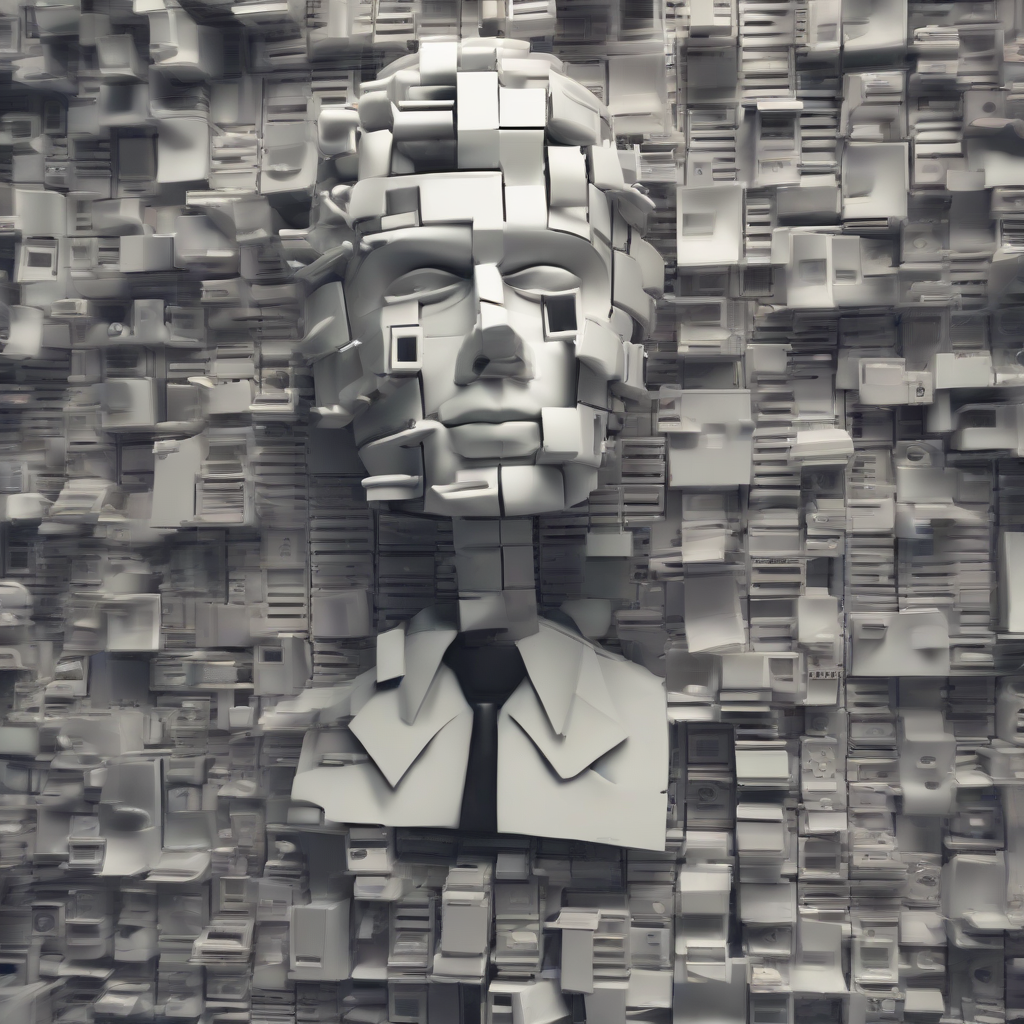
Shell and Tube Heat Exchangers: A Deep Dive into Design, Operation, and Applications
Shell and tube heat exchangers are among the most widely used types of heat exchangers in various industries. Their robust design and versatility make them suitable for a broad range of applications, from power generation and chemical processing to HVAC systems and refrigeration. This comprehensive guide delves into the intricacies of shell and tube heat exchangers, covering their design principles, operational characteristics, and diverse applications.
I. Fundamental Principles of Shell and Tube Heat Exchangers
At their core, shell and tube heat exchangers facilitate heat transfer between two fluids, typically at different temperatures. One fluid flows through a bundle of tubes housed within a cylindrical shell, while the other fluid flows either inside the shell or outside the tubes, depending on the configuration. This counter-current or co-current flow pattern promotes efficient heat transfer between the two fluids.
A. Heat Transfer Mechanisms
- Conduction: Heat transfer occurs through the tube walls and the shell. The material properties of the tube and shell materials significantly impact the rate of heat transfer.
- Convection: Fluid motion within the tubes and shell enhances heat transfer by continually replacing cooler fluid near the heat transfer surfaces with warmer fluid. The fluid velocity and its physical properties (viscosity, thermal conductivity, specific heat) influence convective heat transfer.
- Fouling: Over time, deposits (scale, corrosion products, etc.) can accumulate on the heat transfer surfaces, reducing their effectiveness. Fouling significantly impacts heat transfer efficiency and requires regular cleaning or mitigation strategies.
B. Types of Shell and Tube Heat Exchangers
- Fixed Tube Sheet Exchangers: These are the simplest type, with tubes fixed to the tube sheets at both ends. They are suitable for lower pressure applications.
- U-Tube Exchangers: The tubes are bent into a U-shape, allowing for thermal expansion and contraction without significant stress on the tube sheets. They are often preferred for high-pressure or high-temperature applications.
- Floating Head Exchangers: One tube sheet is fixed, while the other is allowed to move, accommodating thermal expansion and contraction. This design is commonly used for high-pressure and high-temperature applications where thermal expansion is significant.
- Kettle Reboiler Exchangers: A specific type often used in distillation processes where the shell side contains a boiling liquid, and the tubes carry the vapor.
II. Design Considerations for Shell and Tube Heat Exchangers
The design of a shell and tube heat exchanger involves several critical factors to ensure optimal performance and longevity. These include:
A. Heat Transfer Area
The total heat transfer area is directly proportional to the heat transfer rate. The designer must determine the appropriate tube diameter, length, and number to achieve the required heat transfer area. This calculation depends on factors such as the desired heat duty, fluid properties, and temperature differences.
B. Shell and Tube Diameter
The shell diameter and tube diameter are crucial design parameters influencing flow patterns, pressure drop, and heat transfer efficiency. Smaller diameters lead to higher velocities and improved heat transfer but increased pressure drop. Larger diameters result in lower pressure drop but potentially lower heat transfer coefficients.
C. Tube Layout and Baffles
The arrangement of tubes within the shell (triangular, square, or rotated square) and the presence and spacing of baffles significantly impact the flow pattern and heat transfer. Baffles direct the shell-side fluid, increasing the velocity and heat transfer coefficient. Optimal baffle spacing is essential to balance heat transfer and pressure drop.
D. Material Selection
Material selection is crucial for ensuring compatibility with the fluids being handled and operating conditions. Common materials include stainless steel, carbon steel, copper, and alloys tailored to specific corrosion resistance and temperature requirements.
E. Pressure Drop Considerations
Pressure drop in both the shell side and tube side is a critical aspect of design. Excessive pressure drop can lead to increased pumping power requirements and reduced efficiency. Design optimization aims to minimize pressure drop while maintaining effective heat transfer.
III. Operational Aspects of Shell and Tube Heat Exchangers
Efficient operation of shell and tube heat exchangers requires careful consideration of several factors:
A. Flow Rate Control
Maintaining appropriate flow rates for both fluids is crucial for efficient heat transfer. Inadequate flow rates can lead to reduced heat transfer and potential fouling. Flow rate control valves are often used to regulate the flow and maintain optimal operating conditions.
B. Temperature Monitoring
Monitoring the inlet and outlet temperatures of both fluids allows for real-time assessment of heat transfer performance. Deviations from expected temperatures may indicate fouling, leaks, or other operational issues requiring attention.
C. Pressure Monitoring
Regular monitoring of shell-side and tube-side pressures is essential for detecting leaks or blockages. Sudden pressure drops or increases can indicate serious problems that require immediate attention.
D. Cleaning and Maintenance
Regular cleaning and maintenance are vital for maintaining heat transfer efficiency and extending the lifespan of the heat exchanger. Fouling can significantly reduce heat transfer effectiveness, necessitating regular cleaning procedures, such as chemical cleaning or mechanical cleaning using brushes or specialized tools.
IV. Applications of Shell and Tube Heat Exchangers
Shell and tube heat exchangers are employed in a vast array of applications across numerous industries. Their versatility and robust design contribute to their widespread use. Some key applications include:
- Power Generation: Condensing steam in power plants, preheating feedwater, and other crucial processes rely heavily on shell and tube heat exchangers.
- Chemical Processing: Numerous chemical reactions and separation processes utilize shell and tube exchangers for heating, cooling, and temperature control.
- Petroleum Refining: Shell and tube heat exchangers play a critical role in various refinery processes, including distillation, cracking, and heat recovery.
- HVAC Systems: Larger HVAC systems utilize shell and tube exchangers for heating and cooling in commercial and industrial buildings.
- Refrigeration: Shell and tube exchangers are used in various refrigeration cycles for transferring heat between refrigerants and other fluids.
- Food and Beverage Processing: Pasteurization, sterilization, and other temperature-sensitive processes often utilize shell and tube exchangers for efficient heating and cooling.
- Pharmaceutical Manufacturing: Precise temperature control is critical in pharmaceutical manufacturing, and shell and tube heat exchangers provide efficient temperature regulation.
V. Advantages and Disadvantages of Shell and Tube Heat Exchangers
Like any technology, shell and tube heat exchangers have both advantages and disadvantages:
A. Advantages
- High Heat Transfer Efficiency: Their design allows for effective heat transfer between fluids, even with significant temperature differences.
- Robust Construction: They are built to withstand high pressures and temperatures, making them suitable for demanding applications.
- Versatility: They can handle a wide range of fluids and operating conditions.
- Relatively Easy to Clean and Maintain: Cleaning access is generally good, facilitating regular maintenance.
- Wide Range of Sizes and Configurations: Exchangers can be designed and built to meet diverse requirements.
B. Disadvantages
- High Initial Cost: They are often more expensive than other heat exchanger types.
- Large Footprint: Their size can be a significant factor, especially for large capacity exchangers.
- Potential for Fouling: Fouling can reduce efficiency over time and necessitate regular cleaning.
- Complexity of Design and Fabrication: Design and manufacturing require specialized expertise and equipment.
VI. Future Trends in Shell and Tube Heat Exchanger Technology
Ongoing research and development aim to further enhance the performance and efficiency of shell and tube heat exchangers. Key areas of focus include:
- Advanced Materials: Exploring new materials with improved corrosion resistance, higher thermal conductivity, and enhanced fouling resistance.
- Optimized Designs: Utilizing computational fluid dynamics (CFD) and other advanced simulation tools to optimize designs for improved heat transfer and reduced pressure drop.
- Enhanced Manufacturing Techniques: Implementing advanced manufacturing processes, such as additive manufacturing (3D printing), for improved precision and reduced manufacturing time.
- Smart Monitoring and Control: Integrating sensors and control systems to enable real-time monitoring and automated control for improved efficiency and reduced maintenance.